Un nuevo panorama para la Industria en Ecuador
Share
Hace unos años, cuando iniciamos nuestro proceso de “evangelización” sobre cómo abordar en el país una nueva era disruptiva, nos enfrentamos en ese entonces con una industria ecuatoriana aún en fase de negación, la renovación tecnológica era considerada una ruta tortuosa por la que todas las organizaciones debían pasar, con inversiones exorbitantes y resultados poco predecibles.
La penetración de tecnología digital en la vida diaria, el decrecimiento del costo de conectividad, la abundante oferta de servicios en la nube y una conciencia colectiva de estar viviendo una era sin precedentes, han despertado en el empresariado nacional un nuevo punto de vista sobre la productividad, la eficiencia y la generación de valor, terreno fértil para el uso industrial de tecnologías como Internet de las Cosas (IOT), Automatización Robótica de Procesos (RPA) o Inteligencia Artificial (AI).
De la negación pasamos hoy en día a una etapa de reconocimiento. La evidencia de resultados favorables en el despliegue ágil de pilotos digitales abrió un nuevo panorama para el uso y aplicación industrial de tecnología digital:
Sacar el mayor provecho de los activos
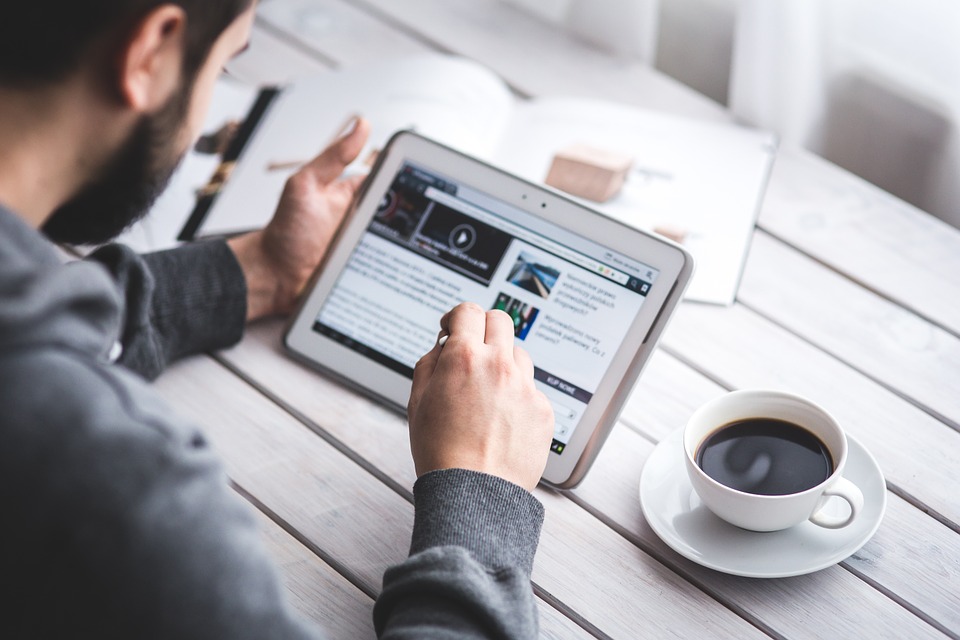
Tradicionalmente el mantenimiento de planta se realiza mediante enfoques preventivos o reactivos. Es muy baja la aplicación de prácticas de mantenimiento basado en condiciones en Ecuador, dada la dificultar de poder identificar advertencias tempranas de la falla y aplicar un enfoque predictivo. Pero ¿qué pasaría si pudiésemos entender de forma precisa el comportamiento real del equipo y ajustar el mantenimiento a lo que realmente se necesita?
El concepto sería poder leer los datos del comportamiento del equipo desde un sensor instalado en el mismo, compararlos con un modelo matemático que describe el funcionamiento normal del equipo, denominado “Gemelo Digital” y analizar las desviaciones para pronosticar cuándo fallará, cuál será el impacto de la falla, qué otros componentes pueden verse afectados y cuándo sería el mejor momento para realizar el mantenimiento, reduciendo costos y planificando de mejor forma la parada.
Perfeccionando el modelo
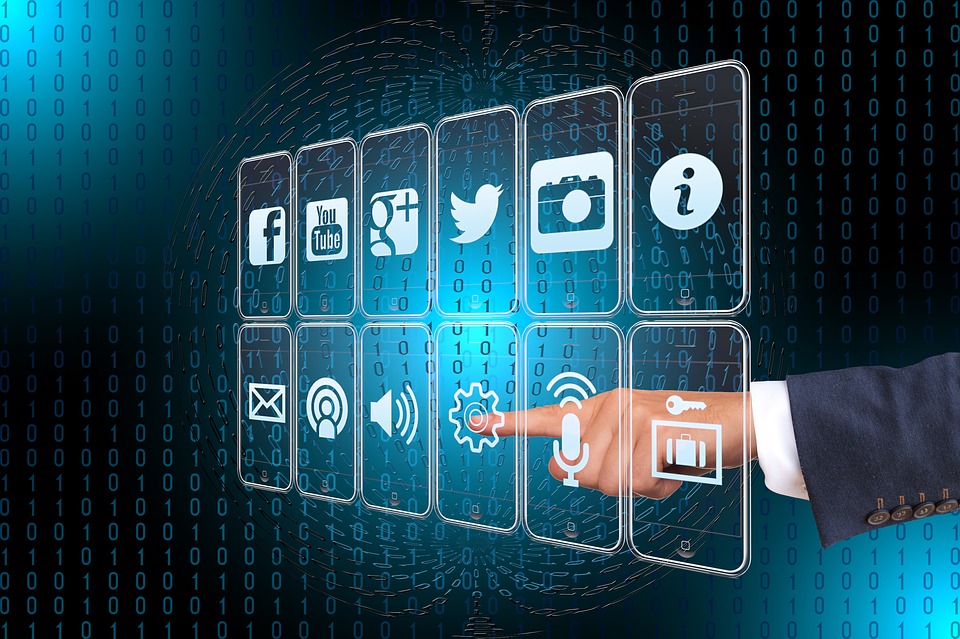
Hoy en día, el desafío ya no está en tener acceso a tecnología sino en la capacidad de construir el modelo correcto, el verdadero “gemelo digital”. Un equipo que ha operado durante algún tiempo y que ya ha pasado por reparaciones tiene un comportamiento diferente al original comprado al fabricante. Hasta hace poco reconstruir la historia del equipo y emular su funcionamiento requería largos procesos de investigación, validación y pruebas antes de poder aplicarlo.
Utilizando IOT y Big Data ya podemos fácilmente recopilar y procesar altos volúmenes de datos del equipo en tiempo real y correlacionarlos de forma dinámica con el historial de mantenimientos y fallas. Mediante inteligencia artificial podemos diseñar y entrenar una red neuronal artificial que puede aprender, alimentar y afinar el modelo de “Gemelo Digital” continuamente.
Y funciona, hemos observado un aumento del tiempo promedio entre fallas (MTBF), un tiempo de inactividad planificado más corto y un impacto positivo en la efectividad general del equipo (OEE). Pero en base a los resultados, es seguro decir que una combinación de datos de sensores con aprendizaje automático puede revolucionar la eficiencia de las operaciones y aumentar significativamente la utilización de activos en planta.